Floor coating instructions
In this guide you will find detailed instructions on how to do one
Epoxy resin floor coating you can make it yourself.
In In many garages or workshops you can see the bare concrete, some of which is already cracked or just plain ugly. Although it is a usable space and therefore it is not a catastrophe, it would certainly be visually nicer and look tidier if a nice floor coating was laid over the garage floor. Furthermore, one of the largeThe disadvantages of the concrete floor are that it becomes stained over time and is also not easy to clean. There are many reasons that speak against the concrete floor and the most common are the visual and cleaning problems. If you have decided that you want to seal your garage floor with epoxy resin - we recommend reading our step-by-step instructions. Here you will find useful tips that will support you in your work and make your work easier. These are the materials you will need for the work:
-
primer
-
Epoxy resin
-
Cleaning agent (acetone), sealing roller, bucket, vacuum cleaner if necessary
-
High-pressure cleaner or water hose with brush.
-
nail shoes
-
Agitator
-
Paint brush
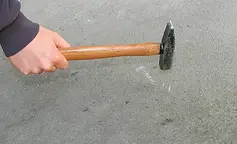
Step #1 - Check the condition of the garage floor
Before the garage floor receives a coating, the concrete floor must be completely cleared. You have to make sure that the floor is completely solid and intact. Damage and hollow spots must be identified and repairedbe leveled, for example with filler or self-leveling repair compound. The strength of the screed or concrete slab can be checked with a hammer or a scratch test. If parts come loose during this check, the floor should first be solidified before coating is carried out. After repairing, the entire surface is sanded.

Step #2 – Clean Garage Floor
Should the floor be dirty spotn, e.g. have oil stains, dirt or paint residue, we strongly recommend removing these by cleaning the garage floor with a special cleaning agent for concrete floors. The floor must be clean and must not show any major damage. This is very important so that the floor coating can adhere. Now some spatula work is required because you have to take a spatula in your hand and scrape off the stubborn and dried dirt from the floor. After this work, take a vacuum cleaner and remove all particles and dust residues from the floor. Take an oil stain remover and use it to remove the remaining oil stains. You can then use a high-pressure cleaner or a water hose from the garden to hose off the remaining dirt from the floor.
If the floor is still dirty, you can use special concrete cleaners. Allow the cleaning agents to take effect for some time and then try to scrub the concrete floor thoroughly with a scrubber. Pulling it off with a rubber lip will help you remove the protective residue left behind, including water, from the garage. Now rinse everything off with fresh water and your garage should now be ready for coating.

Step #3 - The soil must dry out
Before you coat the garage floor, it must be absolutely dry and not even damp. The surface must then dry thoroughly. It is recommended to check the humidity. This is possible, for example, by covering a certain area with foil: If moisture has formed under the foil after 24 hours, the floor has not yet dried sufficiently. New concrete slabs or screeds must dry out for at least 5 weeks before the coating can be applied.

Step #4 – Prime Garage Floor
You cannot coat the floor before priming the highly absorbent substrate as the floor must be waterproof for the coating. The liquid must be mixed well. The primer must be applied evenly with a paint roller as if you were painting the garage floorI would. The coating material must be distributed over the entire floor.
You also have to make sure that the individual tracks do not overlap.
We recommend BFor areas of 20 square meters or smaller, apply 2 thin layers of primer, 2 x 3 kilos.
For the second layer, add 50 grams of pigment paste.
The primer layer usually needs to dry for at least 12 hours.
Caution is advised when there is high humidity and high temperatures. Condensation can cause stains. The ideal processing temperature is between 15 and 25 degrees.

Step No. 5 - Apply floor coating with pigment paste and possibly colored flakes
Take a mixer and start mixing the floor coating.
Mix in 3% pigment paste for a colorful result, start pouring in one corner and work your way out. After you have dumped some of the materials on the ground, SAct quickly by rolling the liquid. You have to roll the liquid into the garage floor, lane by lane.
Make sure that the tracks do not cross each other. The self-leveling layers are particularly easy to process. These can distribute themselves over the surface and at the same time compensate for the unevenness. Work quickly and spread the entire coating on the garage floor without stopping.
Optional: Immediately after coating, sprinkle the colored flakes as evenly as possible onto the floor. This is how so-called pigmentation occurs
It's best to distribute the flakes in 4 portions, coat 1/4 of the base and sprinkle the flakes over it, working steadily until the entire base is finished.
It is then important that you adhere to the prescribed drying time so that the coating can dry out sufficiently.

Optional
When using colored flakes
Step#6 - Apply second coat of floor coating see step #5
We reccomendehlen that after the color chips have been distributed on the epoxy resin, one2nd layerRoll coating is to be applied. The reason for this sealing is that there are no sharp edges. Scattering the paint chips can cause them to stand up, creating sharp edges. By sealing, these edges in particular are broken and a smoother surface is obtained.
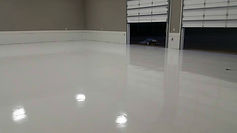
Step #7- Allow coating to cure
The optimal room temperature for drying out is 20 degrees Celsius. The relative humidity should be at least 65 percent. We recommend waiting 7 days before loading the freshly coated floor.
Accessible after approx.24 hours
Chemically cured after approx. 7 days at 20°C
Try to have some patience for this important procedure and don't ruin your own work by entering the garage too early. Your patience will pay off in the end because your garage or the surface is now protected from road salt, motor oil and street dirt.
Please note that high temperatures result in faster curing time.
For this reason, work should be carried out in cool temperatures.
In midsummer, caution should be exercised when working in ground-level rooms. The air is warm and humid. Because the warm and moist air hits a floor that is approximately 15 degrees Celsius cooler, condensation forms, which can lead to unsightly stains. The ideal temperature for such work is between 16 and 23 degrees Celsius.
IMPORTANT:
Please only mix as much epoxy resin as you want to use. As soon as the epoxy resin (resin + hardener) is bonded together, you must work quickly, otherwise the epoxy resin will harden. If the speed is too high, excessive heat can be generated, which in turn can lead to the materials hardening more quickly.
Schritt für Schritt Anleitung-Rollbeschichtung